In 2023, German construction companies lost an estimated €4.7 billion—because they had too much work. Sounds absurd? It’s true. A study by the Institute for the German Economy found that the bottleneck isn’t labor or materials, but logistics. Where to store steel beams when delivery trucks block half the site? How to prep components when there’s no covered space? As demand rises, infrastructure collapses. What if the real solution doesn’t lie in building bigger—but in building smarter?
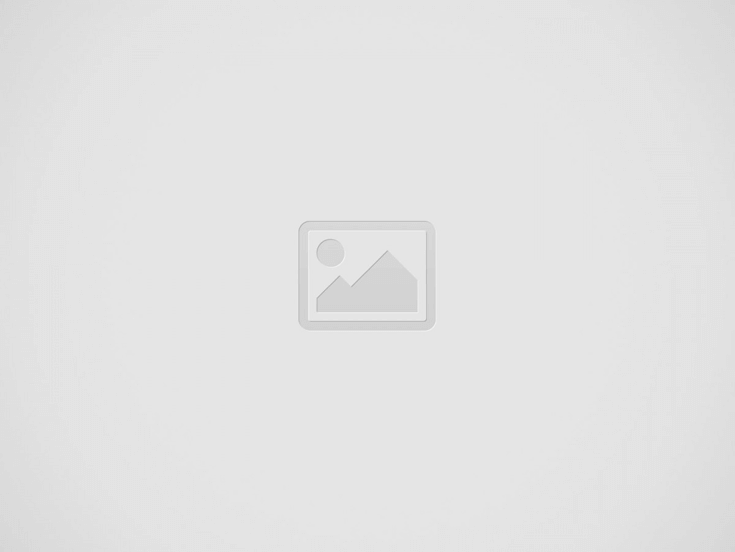
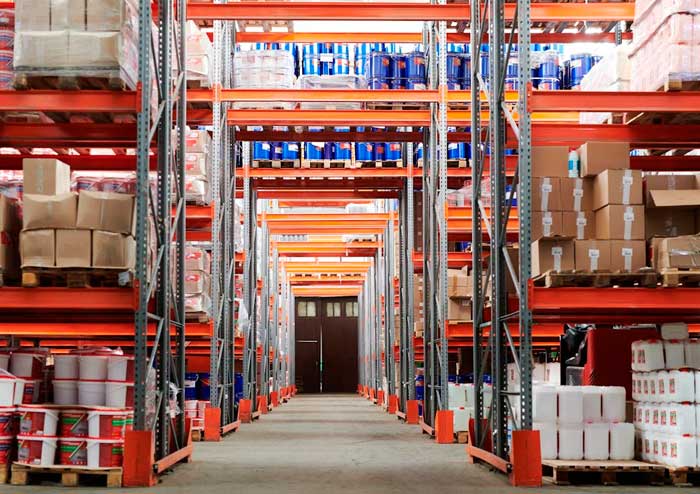
When warehouses become the weak link
Order books are overflowing, crews stand ready—but the crane doesn’t move. No strikes, no supply shortages, no labor disputes. The real issue? Nowhere to store or pre-assemble vital components. On a major construction site outside Cologne, this exact problem brought progress to a halt. A €27 million distribution center sat in limbo for weeks because the planned storage facility was cut from the budget. The cost of a missing roof? Far more than anyone had calculated.
This isn’t an isolated case. As demand grows, infrastructure in many mid-sized firms simply can’t keep up. Job sites turn into traffic jams. Deliveries arrive too early and lie exposed to the elements. Assembly crews idle while parts wait in distant depots. In this race against time, flexibility becomes a decisive factor—and that’s where temporary structures offer a crucial advantage. Fast to deploy, easy to relocate, and tailored to site-specific needs, these modular units provide exactly what’s missing: space to store, work, and adapt.
Permits, paperwork, paralysis
In theory, every project manager knows the value of covered space. In practice, too many get tangled in red tape. Building a permanent warehouse? Expect months of permitting, site surveys, and regulatory checks. For fast-moving projects, that timeline is a deal-breaker. So, materials sit under tarps, if they’re protected at all.
That’s where temporary structures sidestep the trap. Classified differently by most regional authorities, they often require only simplified permits—or none at all, depending on duration and usage. The legal wiggle room can mean the difference between a two-month delay and being operational by next Tuesday.
But regulatory ease is only half the story. The real edge is scalability. When one of Europe’s largest solar park developers faced a sudden capacity crunch mid-project, they turned to modular solutions. A 1,200-square-meter mobile warehouse was delivered and fully operational in under 72 hours—just in time to receive the next freight load of panels. No concrete, no delays, no bureaucratic wrestling.
Thinking beyond concrete
Too often, warehouse planning is stuck in an old industrial mindset: big, heavy, permanent. But modern logistics needs mobility. Spantech, a European leader in modular infrastructure, sees demand shifting fast. “Clients no longer want fixed solutions—they want flexible assets,” says a company spokesperson. Their temporary buildings have been used across sectors: from aerospace to retail, from public works to pop-up medical facilities. It’s a rethink of what space means—and how it should perform under pressure.
Weatherproofing productivity
Rain doesn’t wait. Nor do penalties. Miss a deadline on a highway expansion project, and it’s not just revenue lost—it’s reputation. That’s why exposure risk has become one of the most underestimated threats to construction ROI. Open-air sites turn into mud pits. Components corrode. Safety hazards increase.
A Munich-based prefab builder recently estimated that just seven days of uncontrolled weather exposure added over €180,000 to their cost sheet—through damaged panels, delayed installation, and extra labor. Their lesson? Never treat the storage question as secondary.
Temporary structures offer more than just a roof. Many models now come with full insulation, lighting, and integrated flooring systems—making them usable year-round, in almost any climate. Some are rated for wind speeds up to 150 km/h. In the north of Sweden, one firm even used a heated modular hall to pre-assemble tunnel elements in -20°C.
Infrastructure that adapts to growth
There’s a myth in business that scaling is just a question of more: more staff, more machines, more square meters. But in fast-growing industries like renewables, logistics, and e-commerce construction, space isn’t just a static asset—it’s a dynamic resource.
During the pandemic, several manufacturers pivoted overnight—from car parts to ventilator casings, from furniture to plexiglass shields. What made those pivots possible? Access to reconfigurable, modular infrastructure that didn’t require a three-year building permit.
The same logic applies to warehouse construction. Traditional builds are slow, costly, and often over-engineered for what’s needed in the moment. Temporary structures, in contrast, scale with demand. Need an extra 600 sqm for six months? Done. Need it moved across the site next quarter? No problem.