Pittsburgh – A group of researchers at Carnegie Mellon University designed a method of 3-D printing for artificial tissues and organs that can possibly be a game changer for patients waiting in transplant lists.
For many years, 3D printers have been used to print hard objects with layers of plastic or metal that slowly construct the objects, but researchers have struggled with printing soft tissues such as organs since the materials used for them can’t support their own weight. After buying a consumer-level 3-D printer by the affordable amount of $1,000, they proceed to hack it to print soft materials by layering them with another specially designed type of gel.
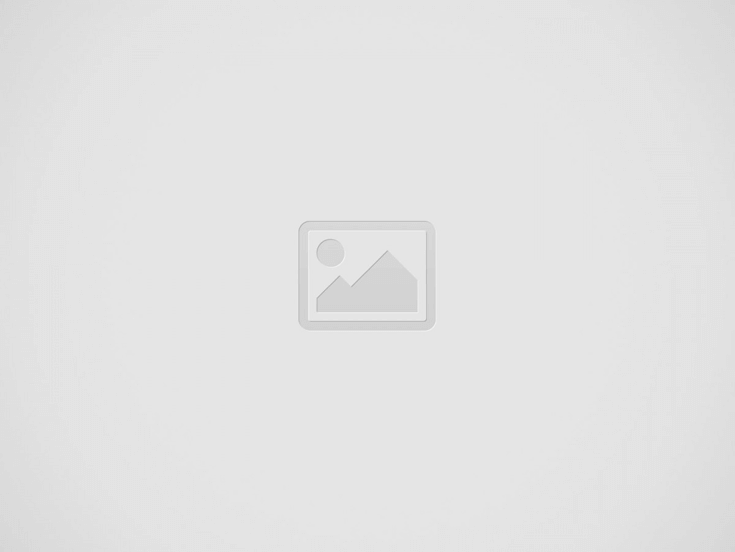
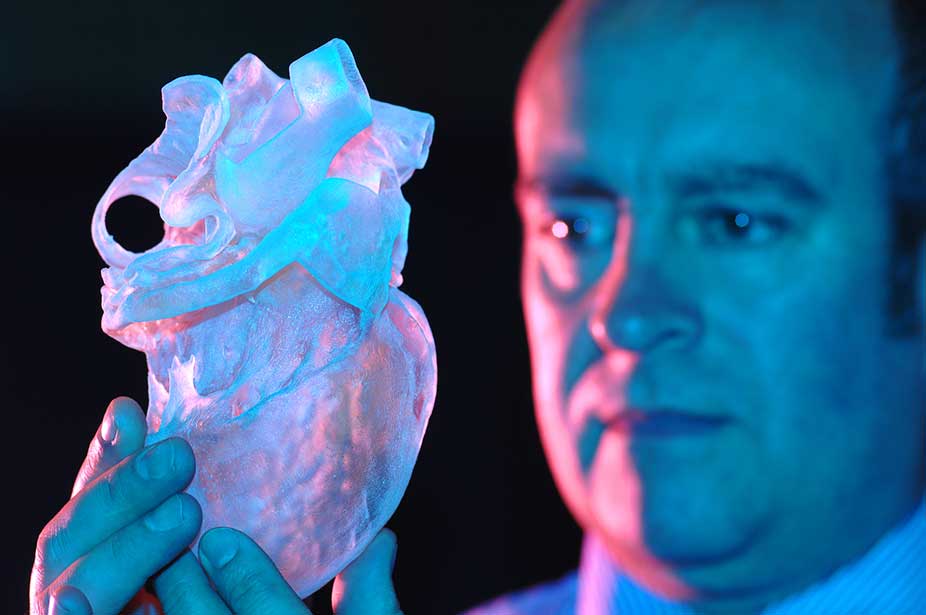
“The challenge with soft materials, think about something like Jello that we eat, is that they collapse under their own weight when 3-D printed in air,” Adam Feinberg, lead author of the study, said in a press release.
The researchers developed a printing method called FRESH, or “Freeform Reversible Embedding of Suspended Hydrogels,” that starts with an appropriate-sized container of support gel. The printer, armed with a needle, injects other gels into the support gel based on computer-aided design models.
Feinberg reported to UPI they developed a method of printing these soft materials inside a support bath material. Essentially, they print one gel inside of another gel, which allows them to accurately position the soft material as it’s being printed layer-by-layer.
Once the structure is completed, the supported gel is melted, leaving only the soft object that had been printed. In tests, the researchers created femurs, branched coronary arteries, trabeculated embryonic hearts, and human brains using the method.
For researchers, is not only about the low costs but about the open-source software which can optimize what they’re doing and maximize the quality of what they’re printing.
Source: UPI